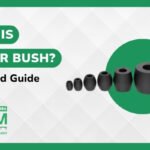
What is Rubber Bush? A Detailed Guide
February 6, 2025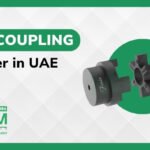
Jaw Coupling Supplier in UAE
February 17, 2025Introduction
Jaw couplings are simple mechanical parts used to connect two shafts while smoothly transferring power. They reduce shocks, lower vibrations, and adjust for minor misalignment, making them perfect for industrial equipment like pumps, compressors, and conveyors.
At Manglam Engineers, we provide high-quality Jaw Couplings in Doha made to meet the needs of industries in Doha. Our strong and reliable products help keep your machines running smoothly and efficiently.
What Are Jaw Couplings?
Jaw couplings are a type of mechanical coupling used to connect two shafts while transmitting torque. They are designed to absorb shock and accommodate misalignment, making them ideal for various industrial applications, including pumps, compressors, conveyors, and mixers.
Key Components of Jaw Couplings
- Two Metal Hubs: Connect to the shafts and transfer torque.
- Elastomer Spider: Fits between the hubs to absorb shock, vibration, and compensate for misalignment.
- Jaws: Interlock with the spider to ensure smooth torque transmission between hubs.
- Fasteners: Secure the hubs on shafts using set screws or clamping bolts.
Types of Jaw Couplings
- Standard Jaw Couplings: Suitable for general-purpose applications with moderate torque and flexibility.
- Curved Jaw Couplings: Provide higher torque capacity and improved vibration damping.
- Spacer Jaw Couplings: Allow greater distance between connected shafts.
- Zero-Backlash Jaw Couplings: Ensure high precision and no play, ideal for servo and robotic applications.
- Split Hub Jaw Couplings: Simplify installation and removal without disturbing existing components.
Jaw Coupling
Benefits of Jaw Couplings
Jaw couplings help transfer power smoothly while reducing vibrations and handling minor misalignment. They are strong, reliable, easy to install, and budget-friendly.
- Vibration Absorption: The elastomer spider absorbs shocks and vibrations, protecting machine parts.
- Alignment Flexibility: Handles slight misalignment between connected shafts, including angular, parallel, and axial shifts.
- Wide Use: Suitable for various industries like pumps, conveyors, and automated systems.
- Long-Lasting: Built with strong materials to work well even in tough conditions.
- Easy Maintenance: Simple design allows for quick assembly and part replacement.
- Affordable: Provides reliable performance at a reasonable cost.
- Power Transfer: Effectively transfers power between shafts with minimal loss.
- Flexible Options: Available in different types and sizes for various needs.
- Reliable Operation: Can keep running even if the elastomer spider wears out, avoiding sudden breakdowns.
Applications of Jaw Couplings
Jaw couplings are widely used in various industries due to their reliability and flexibility:
- Pumps and Compressors: Used to connect motors to pump shafts for fluid movement.
- Alignment Flexibility: Handles slight misalignment between connected shafts, including angular, parallel, and axial shifts.
- Wide Use: Suitable for various industries like pumps, conveyors, and automated systems.
- Long-Lasting: Built with strong materials to work well even in tough conditions.
- Easy Maintenance: Simple design allows for quick assembly and part replacement.
- Affordable: Provides reliable performance at a reasonable cost.
- Power Transfer: Effectively transfers power between shafts with minimal loss.
- Flexible Options: Available in different types and sizes for various needs.
- Reliable Operation: Can keep running even if the elastomer spider wears out, avoiding sudden breakdowns.
Advantages of Using High-Quality Jaw Couplings
Jaw couplings connect two rotating shafts and help transfer power between them. Using high-quality versions offers several key benefits:
1. Reduces Vibrations and Noise
They help make machines run more smoothly by cutting down on vibrations and noise.
2. Handles Misalignment
These couplings adjust when the shafts aren’t perfectly aligned, protecting parts from damage.
3. Absorbs Shocks
They soften sudden force changes during operation, reducing strain on machine parts.
4. Long-Lasting and Tough
Built with strong materials, they resist wear, damage, and harsh environments, lasting longer.
5. Efficient Power Transfer
They transfer power between parts without slipping, keeping machines working precisely.
6. Easy to Install and Maintain
Jaw couplings are simple to set up and need little maintenance, saving time and money.
7. Safety Backup Feature
Even if the flexible part breaks, they can temporarily keep the machine running.
8. Works in Many Industries
They come in different sizes and types for use in manufacturing, robotics, and other fields.
Investing in good-quality jaw couplings helps machines run better, last longer, and save money in the long run.
How to Choose the Right Jaw Coupling
Selecting the right jaw coupling is essential for smooth and reliable operation. Keep these key points in mind:
1. Understand Application Needs:
- Identify the torque, speed, and load conditions.
- Consider vibration levels and shock loads during operation.
2. Select the Proper Size:
- Match the shaft diameter and torque capacity requirements.
- Ensure the coupling size can handle the expected system load.
3. Choose Suitable Material:
- For harsh environments, use corrosion-resistant materials.
- Select heat-resistant materials for high-temperature applications.
4. Check Misalignment Handling:
- Pick a coupling that accommodates angular, parallel, and axial misalignments.
5. Consult a Specialist:
- Get advice from experts or trusted suppliers like Manglam Engineers to find the right fit for your system.
Maintenance Tips for Jaw Couplings
Keep your jaw couplings in top condition by following these simple tips:
1. Regular Visual Inspection:
- Check for signs of wear, cracks, or deformation in the elastomer spider and hubs.
- Ensure all components are free from dirt, corrosion, and debris.
2. Monitor Alignment:
- Verify the alignment of shafts to avoid excessive stress on the coupling.
- Correct any misalignment to prolong the lifespan of the coupling.
3. Lubrication Check:
- Jaw couplings typically do not require lubrication, but ensure the operating environment is clean and dry.
4. Tighten Fasteners:
- Check set screws, clamping bolts, or other fastening components regularly.
- Ensure they remain secure to prevent slippage.
5. Replace Elastomer Spider:
- Replace the spider if it shows signs of wear or hardening to maintain performance.
6. Check for Vibrations:
- Investigate and address unusual vibrations as they may indicate coupling damage or misalignment.
7. Follow Manufacturer Guidelines:
- Adhere to specific maintenance schedules and procedures provided by the manufacturer.
8. Spare Parts Readiness:
- Keep spare spiders and fasteners readily available for quick replacements.
Manglam Engineers — Trusted Jaw Coupling Suppliers in Doha
At Manglam Engineers, we are committed to providing high-performance Jaw Couplings in Doha and other mechanical components to meet the demands of industries in Doha. Our products are designed to offer unmatched performance, reliability, and longevity.
Why Doha Industries Trust Us
- Proven track record of excellence
- High-quality materials and manufacturing processes
- Tailored solutions for diverse applications
- Reliable customer support
Conclusion: Get the Best Jaw Couplings from Trusted Experts in Doha
If you're searching for dependable Jaw Coupling suppliers in Doha, Contact Manglam Engineers today for expert guidance and high-quality products.
Contact us to explore how we can meet your needs in Doha, and how we can meet your needs in Doha, Qatar.