
Rubber Bush Supplier In Dubai
March 3, 2025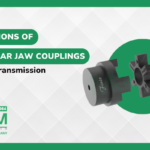
Applications of Spider Star Jaw Couplings in Power Transmission
March 19, 2025Introduction
O-rings might seem like small components, but they play a huge role in keeping machines working properly. Think of them as tiny heroes that prevent leaks in everything from your water bottle to car engines. These round rubber rings create tight seals that keep liquids and air from leaking out where they shouldn't.
In this guide, we'll explore three popular types of rubber O-rings: Silicone, Nitrile, and EPDM. Each has special powers that make them perfect for different jobs. Understanding their unique properties will help you make better decisions for your specific applications.
Making the right choice between these materials can extend equipment life, improve safety, and save money.
Rubber O-Ring Types
Before we compare our three main materials, let's quickly look at the common types of O-rings available:
- Silicone O-rings - Great for extreme temperatures from -65°C to 230°C. Excellent resistance to UV and ozone, but poor with oils and fuels.
- Nitrile O-rings - Excellent with oils, fuels, and hydraulic fluids. Cost-effective option with good abrasion resistance but limited temperature range (-40°C to 120°C).
- EPDM O-rings - Weather-resistant champions with excellent water and steam resistance. Great for outdoor applications but should never be used with oils or petroleum products.
- Neoprene O-rings - Good all-rounders with moderate chemical resistance and temperature range (-40°C to 120°C). Offers good balance of properties at reasonable cost.
- Polyurethane O-rings - Super strong with excellent abrasion and tear resistance. Higher tensile strength than most rubber compounds but limited temperature resistance.
- PTFE O-rings - Chemical superheroes with almost universal chemical resistance. Very low friction coefficient but poor elasticity requires special gland designs.
- Natural Rubber (NR) O-Rings - High elasticity and good tear strength at low cost. Limited chemical resistance and temperature range but excellent for water-based applications.
- Viton® O-rings - Superior chemical and high-temperature resistance (up to 250°C). Excellent for automotive fuel systems and chemical processing but more expensive than standard materials.
- Hydrogenated Nitrile (HNBR) O-Rings - Enhanced temperature resistance over standard nitrile (up to 150°C). Maintains oil resistance while offering better ozone and weathering performance.
- Kalrez® (FFKM) O-Rings - Premium performers with nearly universal chemical resistance and high temperature capability (up to 327°C). Extremely expensive but unmatched in harsh environments.
Silicone, Nitrile, or EPDM? A Complete O-Ring Selection Guide
1. Silicone O-Rings: The Temperature Champion
Silicone O-rings are like the temperature superstars of the O-ring world. They can handle both very hot and very cold conditions without breaking a sweat.
Key Properties:
- Temperature range: -65°C to 230°C (-85°F to 450°F)
- Great flexibility even when cold
- Excellent resistance to ozone, UV light, and oxygen
- Low compression set (keeps its shape well)
Best Applications:
- Medical equipment
- Food processing machinery
- Outdoor equipment
- Appliances
- Electronics
Limitations:
- Not great with oils and fuels
- Lower tear strength compared to other materials
- Can be a bit pricier than basic options
2. Nitrile O-Rings: The Oil-Resistant Performer
Nitrile (also called NBR or Buna-N) is the popular kid in the O-ring class. It's used everywhere because it works well with oils and doesn't cost too much.
Key Properties:
- Temperature range: -40°C to 120°C (-40°F to 250°F)
- Excellent resistance to oils, fuels, and hydraulic fluids
- Good abrasion resistance
- Cost-effective option
Best Applications:
- Automotive systems
- Hydraulic systems
- Fuel handling equipment
- Air compressors
- General industrial equipment
Limitations:
- Not great for extreme temperatures
- Doesn't handle weather exposure well
- Less flexible in cold temperatures
3. EPDM O-Rings: The Weather and Water Specialist
EPDM (Ethylene Propylene Diene Monomer) O-rings are the weather warriors. They can handle sun, rain, and harsh chemicals like cleaning products.
Key Properties:
- Temperature range: -50°C to 150°C (-60°F to 300°F)
- Excellent resistance to weather, ozone, and UV light
- Great with water, steam, and alkalis
- Good electrical insulation properties
Best Applications:
- Water systems
- Steam applications
- Outdoor equipment
- Brake systems
- Appliances
Limitations:
- Poor resistance to oils and fuels
- Not recommended for petroleum applications
- Less resistant to some solvents

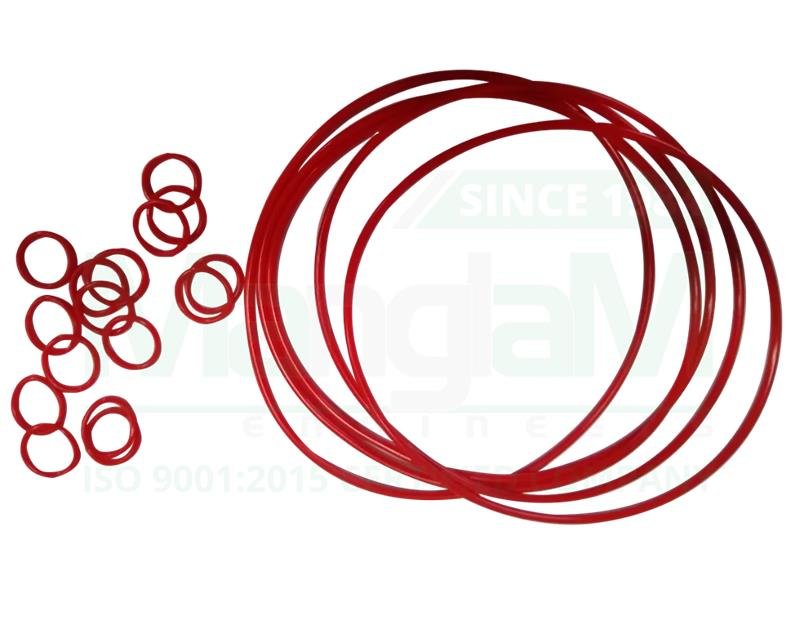
Factors to Consider When Choosing O-Ring Material
Picking the right O-ring isn't just about grabbing any rubber circle. Think about these important factors:
- 1. Operating Temperature: What's the hottest and coldest temperature your O-ring will face?
- 2. Chemical Exposure: Will the O-ring touch oils, fuels, water, or chemicals?
- 3. Pressure Requirements: How much pressure must the O-ring withstand?
- 4. Weather Exposure: Will it be inside or outside facing sun, rain, and temperature changes?
- 5. Cost Considerations: What's your budget? Some materials cost more than others.
- 6. Compression Set: How important is it that the O-ring returns to its original shape?
- 7. Durability Needs: How long must the O-ring last before replacement?
- 8. Industry Standards: Are there specific certifications needed (like FDA approval for food contact)?
Still unsure which O-ring to choose? Contact us for expert advice and get the best solution for your needs.
How to Select the Best Type of O-Ring for Your Needs
Finding your perfect O-ring match is easier than you might think. Follow these simple steps:
1. Identify Your Operating Environment
Make a list of everything your O-ring will encounter:
- Temperature range
- Chemicals or fluids
- Indoor or outdoor use
- Pressure conditions
2. Prioritize Your Requirements
Some properties matter more than others for your specific application. Rank what's most important:
- Chemical resistance
- Temperature resistance
- Cost
- Durability
- Compression set
3. Consult Compatibility Charts
Many manufacturers (like Manglam Engineers) provide charts showing which materials work with various chemicals and conditions.
4. Request Samples When Possible
Testing a sample in your actual application is always best before making a big purchase.
5. Consider Long-Term Value
Sometimes paying more upfront for a premium material saves money by avoiding frequent replacements.
A Comparison of Silicone vs. Nitrile vs. EPDM
Let's put our three rubber champions side by side to see how they stack up:
Property | Silicone | Nitrile | EPDM |
---|---|---|---|
Temperature Range | -60°C to 230°C | -40°C to 120°C | -50°C to 150°C |
Oil & Fuel Resistance | Poor | Excellent | Poor |
Weather Resistance | Good | Good | Excellent |
Water/Steam Resistance | Good | Good | Excellent |
UV & Ozone Resistance | Excellent | Poor | Excellent |
Cost | High | Low | Low-Medium |
Compression Set Resistance | Good | Good | Good |
UV & Ozone Resistance | Poor | Good | Good |
Flexibility | Excellent | Good | Very Good |
Color Options | Many | Limited | Limited |
Choosing the Right O-Ring Supplier
The quality of your O-ring depends greatly on who makes it. Here's how to find a reliable supplier:
1. Look for Manufacturing Experience
Companies like Manglam Engineers have decades of experience creating quality O-rings for various industries.
2. Check for Quality Certifications
Reliable suppliers follow international standards and have certifications to prove their quality.
3. Evaluate Material Options
Good suppliers offer multiple material options and can help you choose the best one for your needs.
4. Consider Custom Capabilities
Sometimes you need special sizes or compounds. Can your supplier create custom solutions?
5. Review Customer Feedback
What do other customers say about the supplier's products and service?
6. Assess Technical Support
The best suppliers provide expert advice to help you select the right O-ring for your specific application.
Conclusion
Choosing between silicone, nitrile, and EPDM O-rings doesn't have to be complicated. Each material has its strengths that make it perfect for specific jobs.
Remember the basics:
- Choose silicone for extreme temperatures
- Pick nitrile when oils and fuels are involved
- Select EPDM for outdoor applications and water systems
By considering your specific requirements and understanding these materials, you can select the perfect O-ring for your application. And when in doubt, consult with experts like Manglam Engineers who can guide you to the right choice.
The humble O-ring may be small, but choosing the right one makes a big difference in how well your equipment works and how long it lasts!