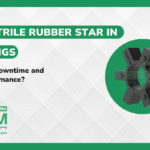
How Nitrile Rubber Star in Couplings Can Lower Downtime and Boost Performance?
June 5, 2025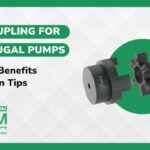
Jaw Couplings for Centrifugal Pumps: Features, Benefits & Selection Tips
June 16, 2025Polyurethane (PU) coupling stars excel in high-torque, heavy-duty applications with superior tear resistance and longer lifespan. Nitrile rubber coupling stars offer excellent chemical resistance and cost-effectiveness for moderate-duty industrial applications.
Choose PU when: You need maximum durability, high torque transmission, or extreme temperature resistance.
Choose Nitrile when: Chemical exposure is a concern, budget is tight, or operating temperatures are moderate.
Both materials serve critical roles in mechanical power transmission systems, but understanding their unique properties ensures optimal machine performance and cost-effectiveness.
What is a Rubber Coupling Star?
A rubber coupling star, also known as a spider coupling insert, is the elastomeric element that sits between two metal coupling hubs in flexible shaft couplings. This star-shaped component absorbs vibrations, accommodates minor misalignments, and transmits torque between connected shafts.
Key Functions:
- Torque transmission between driving and driven equipment
- Vibration damping to reduce machinery stress
- Misalignment compensation for angular, parallel, and axial variations
- Shock absorption during startup and load changes
The coupling star is the heart of jaw couplings, spider couplings, and various flexible mechanical couplings used across industries worldwide.
Material Overview: Polyurethane (PU) vs. Nitrile Rubber (NBR) in Coupling Stars
This material comparison highlights the key specifications that influence coupling star performance, helping engineers choose the right material for specific industrial conditions.
Polyurethane (PU) Coupling Stars
Material Characteristics:
- Hardness Range: 75-98 Shore A
- Temperature Range: -40°C to +80°C (up to +120°C for special grades)
- Tensile Strength: 35-55 MPa
- Elongation: 400-600%
Key Advantages:
- Exceptional tear and abrasion resistance
- High load-bearing capacity
- Superior resilience and fatigue resistance
- Extended service life in demanding applications
Nitrile Rubber (NBR) Coupling Stars
Material Characteristics:
- Hardness Range: 70-90 Shore A
- Temperature Range: -30°C to +100°C
- Tensile Strength: 10-25 MPa
- Elongation: 200-400%
Key Advantages:
- Outstanding oil and fuel resistance
- Excellent chemical compatibility
- Cost-effective manufacturing
- Good compression set resistance
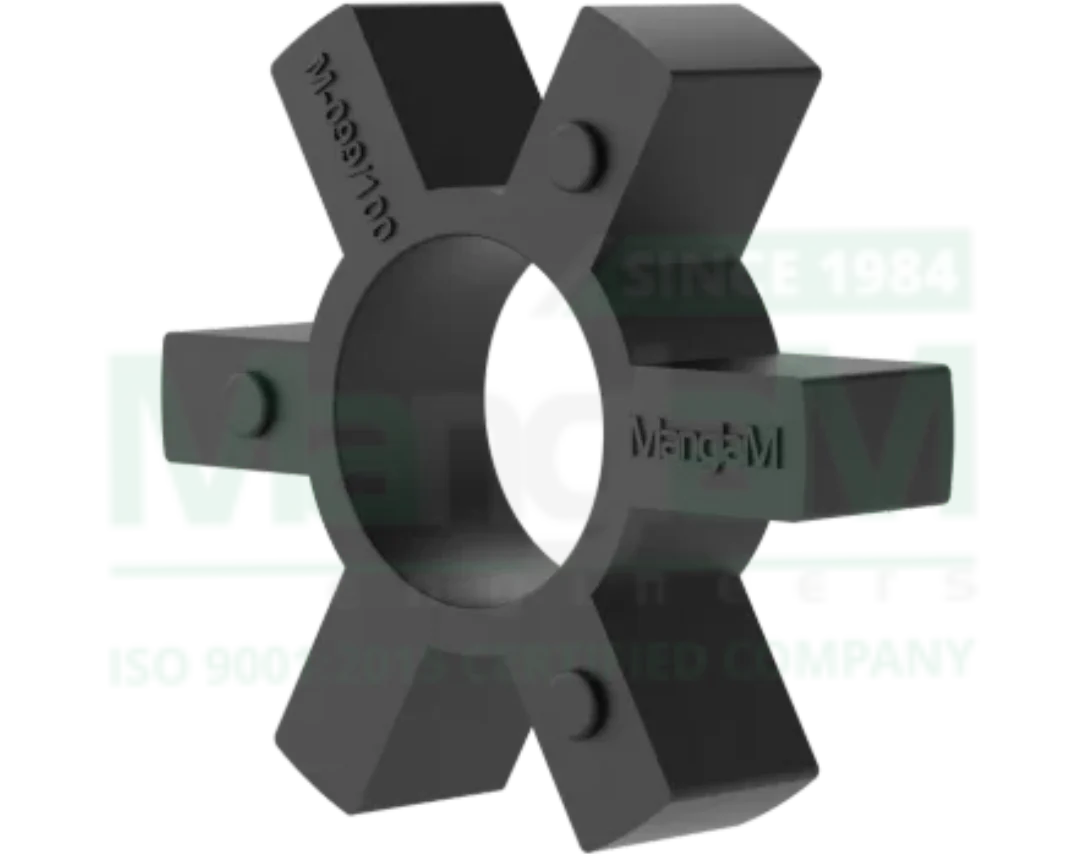
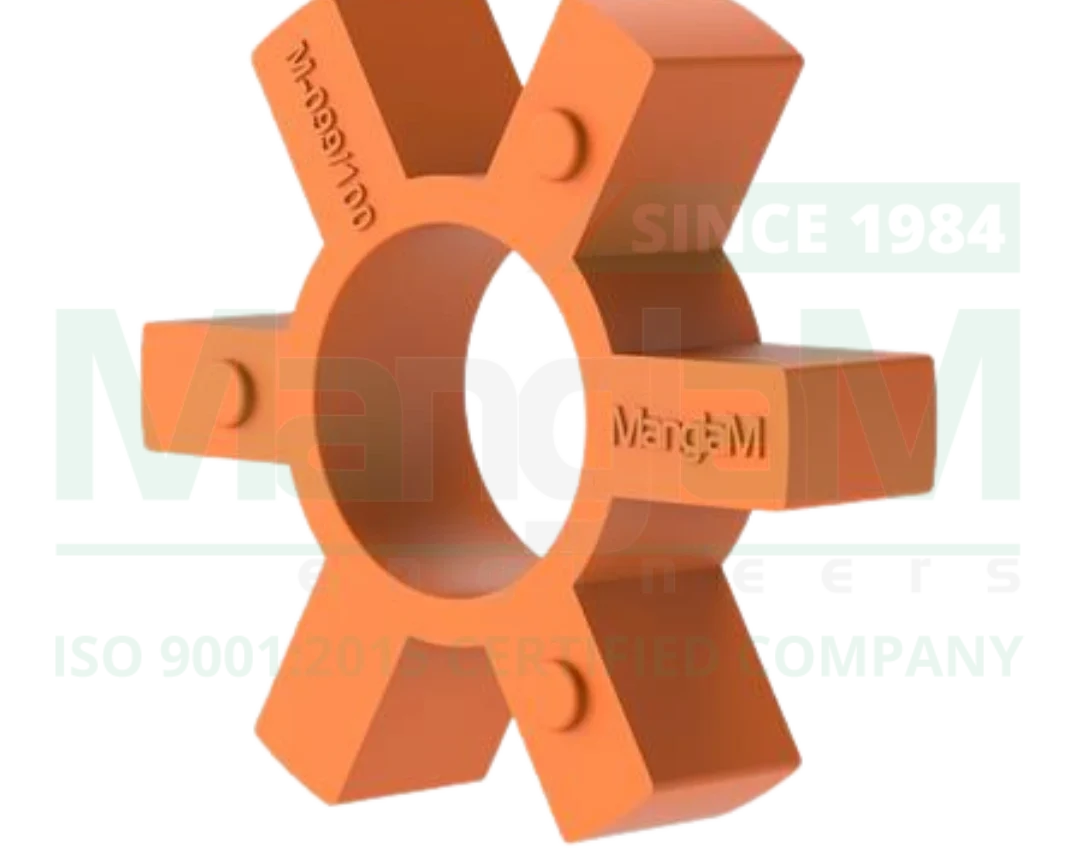
Key Differences Between PU and Nitrile Coupling Stars
This table compares key performance factors to help you choose the right material based on reliability, maintenance needs, and overall cost.
Property | PU Coupling Stars | Nitrile Coupling Stars |
---|---|---|
Durability | Superior (2-3x longer life) | Good for moderate duty |
Chemical Resistance | Limited to specific chemicals | Excellent with oils/fuels |
Temperature Range | Wider (-40°C to +120°C) | Standard (-30°C to +100°C) |
Cost | Higher initial investment | More economical upfront |
Torque Capacity | Higher torque handling | Moderate torque applications |
Vibration Damping | Excellent shock absorption | Good vibration isolation |
Wear Resistance | Outstanding abrasion resistance | Moderate wear resistance |
Industrial Applications and Use Cases
Real-world examples show where each material performs best—and how the wrong choice can cause failures and downtime. Use these scenarios to avoid costly mistakes and choose the right material.
When to Use PU Coupling Stars: Best Applications and Industries
Heavy-Duty Industrial Applications:
- Mining equipment with high shock loads
- Steel mills and metal processing machinery
- Construction equipment in harsh environments
- Marine propulsion systems requiring durability
- High-speed machinery with continuous operation
Specific Industries:
- Cement and aggregate processing
- Power generation facilities
- Heavy manufacturing and forging
- Oil drilling and extraction equipment
When to Use Nitrile Coupling Stars: Use Cases and Industry Applications
Chemical Processing Applications:
- Pump systems handling oils and chemicals
- Refinery equipment with hydrocarbon exposure
- Chemical manufacturing with solvent contact
- Automotive systems exposed to fuels and lubricants
- Food processing with oil-based products
Specific Industries:
- Petrochemical and refining
- Automotive manufacturing
- Food and beverage processing
- Chemical and pharmaceutical production
How to Select the Right Rubber Coupling Star for Your Equipment
Follow these three key steps to choose the right material and avoid failures or downtime. This clear process removes guesswork and ensures reliable, application-specific selection.
Step 1: Analyze Operating Conditions
Temperature Assessment:
- PU for extreme temperatures (-40°C to +120°C)
- Nitrile for standard operations (-30°C to +100°C)
Chemical Exposure Evaluation:
- Nitrile for oil/fuel contact (excellent resistance)
- PU for dry or water-based environments (limited chemical resistance)
Step 2: Calculate Load Requirements
Torque and Power Considerations:
- High torque applications: Choose PU for superior strength
- Moderate torque systems: Nitrile provides adequate performance
- Variable loads: PU offers better fatigue resistance
Step 3: Budget and Lifecycle Analysis
Initial Cost vs. Total Cost of Ownership:
- PU coupling stars: Higher upfront, lower maintenance costs
- Nitrile coupling stars: Lower initial cost, more frequent replacement
PU vs. Nitrile Coupling Stars - Performance Comparison Table
Performance Factor | PU Stars | Nitrile Stars | Winner |
---|---|---|---|
Service Life | 2–4 years | 1–2 years | PU |
Chemical Resistance | Limited | Excellent | Nitrile |
Temperature Stability | Superior | Good | PU |
Shock Absorption | Excellent | Good | PU |
Cost Effectiveness | Long-term | Short-term | Depends |
Maintenance Frequency | Low | Moderate | PU |
Load Capacity | High | Moderate | PU |
Cost Analysis: Is PU or Nitrile More Cost-Effective Over Time?
Understanding total cost of ownership helps balance performance with budget. This analysis compares upfront costs with long-term expenses like replacements and downtime to guide smarter material choices.
Total Cost of Ownership Breakdown
PU Coupling Stars:
- Initial Cost: 150-200% of nitrile equivalent
- Replacement Frequency: Every 2-4 years
- Downtime Costs: Reduced due to longer service life
- Total 5-Year Cost: Often lower despite higher initial investment
Nitrile Coupling Stars:
- Initial Cost: Base reference point
- Replacement Frequency: Every 1-2 years
- Downtime Costs: Higher due to frequent replacements
- Total 5-Year Cost: May exceed PU due to maintenance cycles
Best Value Strategy: Choose based on application criticality and operating environment rather than initial cost alone.
Maintenance Tips: How to Extend the Life of PU and Nitrile Coupling Inserts
Proper maintenance extends coupling star life and prevents costly breakdowns. Each material needs specific care—follow these strategies to ensure reliability and maximize ROI.
Extending Coupling Star Life
PU Coupling Maintenance:
- Monitor for cracking in high-temperature applications
- Check alignment to prevent premature wear
- Inspect for chemical contamination
- Replace when hardness increases significantly
Nitrile Coupling Maintenance:
- Assess chemical compatibility regularly
- Monitor for swelling in chemical environments
- Check for oil saturation and degradation
- Replace when flexibility decreases
Pro Tip: Implement predictive maintenance schedules based on material properties and operating conditions for optimal uptime.
Expert Recommendations
Industry Best Practices: Expert Tips
For OEMs and Plant Engineers:
- Conduct material testing under actual operating conditions
- Factor in total cost of ownership beyond initial purchase price
- Consider future expansion and changing operational requirements
- Work with experienced suppliers for technical guidance
Manglam Engineers' Recommendation: With 40+ years of experience in mechanical power transmission, we recommend:
- PU coupling stars for critical, high-duty applications
- Nitrile coupling stars for chemical processing environments
- Custom material formulations for specialized requirements
Quality and Sourcing: What to Look for in a Reliable Coupling Supplier
Choose suppliers who provide:
- Consistent material properties across production batches
- Technical documentation with performance specifications
- Application engineering support for optimal selection
- Global supply chain capabilities for international operations
Actionable Takeaways: How to Decide Between PU and Nitrile Couplings
Key Decision Points:
- Material Selection: Base choice on primary operating challenges (chemical exposure vs. mechanical stress)
- Cost Strategy: Evaluate total cost of ownership over 3-5 years, not just initial price
- Supplier Partnership: Work with experienced manufacturers who understand your industry requirements
- Preventive Maintenance: Implement material-specific maintenance protocols for optimal performance
- Future Planning: Consider evolving operational requirements when making material decisions
Next Steps:
- Assess your current coupling performance and failure modes
- Calculate total cost of ownership for both materials
- Request samples for testing under actual operating conditions
- Partner with qualified suppliers for ongoing technical support
Ready to optimize your coupling performance? Contact Manglam Engineers at +91 78744 79699 or info@manglamengineers.com for expert guidance on selecting the ideal coupling stars for your specific applications. With 40+ years of experience and 500+ high-quality products, we deliver reliable solutions worldwide.